Expertorial: Rapid Prototyping KYDEX® Thermoplastics Seatback for Rail Interiors
10/9/2023
KYDEX® Thermoplastics offer ample design flexibility while meeting the most stringent fire, smoke, heat release, and toxicity requirements. As a lightweight and durable alternative to FRP, KYDEX® Thermoplastics are not only graffiti resistant, but offer unlimited design possibilities for shape, color, and embossed features, including texture.
As a globally recognized leader in high-performance specialty polymers for mass transit interiors, KYDEX® Thermoplastics provide long-term durability and weight savings over FRP, aluminum, or steel, making them the sustainable choice for customers who expect rail cars to last 20 years or more. With the rolling stock industry growing worldwide, the rail industry is in a position to become more sustainable through the material selection process. As a replacement to FRP, thermoplastics can transform rail car interiors to improve the passenger experience.
The SEKISUI KYDEX mass transit interiors team set out to showcase how thermoplastics can provide better aesthetics, enhanced durability, and improved sustainability for the rolling stock interiors.
To do this, the designLab™, appLab™, business development teams, and SEKISUI KYDEX summer interns from the Pennsylvania College of Technology, Plastics, and Polymers program collaborated to create a pressure-formed sample using PVDF capped KYDEX® 2200LT rail material with Infused Imaging™ technology. The mass transit prototype project offered an opportunity to educate the interns on the rapid prototyping process while creating an educational tool for customers to illustrate different thermoforming processes within one part.
“Our internships give students the opportunity to work on real projects as part of the learning process. This project is an excellent way for our interns to get hands on experience in the field they are interested in, while also providing us with an educational tool for use with customers. The final part provided a physical sample of how KYDEX® Thermoplastics perform in different thermoforming processes,” said Shawn Gum, Business Development Engineer. To kick off the project, a competition was held among the interns to design and present mass transit-inspired parts for consideration, and Elijah Peltz’s design for a mini seatback with the KYDEX® Thermoplastics logo was ultimately selected.
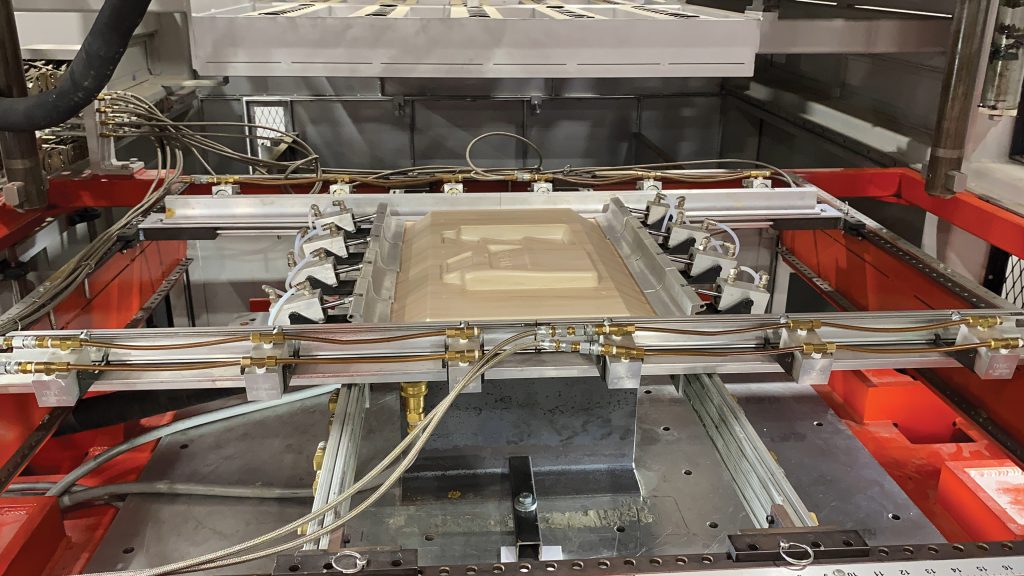
During his experienceship, Peltz learned to program design for both RenShape® and aluminum tools. Ideally, the final tool would be made from aluminum because the molds are temperature controlled and provide better consistency from part to part. They are also more durable and can be used for thousands of parts. RenShape® is an inexpensive polyurethane modeling, and styling board that can be quickly and easily CNC routed into specific shapes but is not temperature controlled. Although the temperature of the mold can fluctuate over time, and the part dimensions can vary from part to part, it is ideal for rapid prototyping.
The initial parts pulled were excellent talking pieces for the InnoTrans Summit. “Several seat manufacturers I visited at InnoTrans were impressed with the design capabilities of the thermoformed mini seatback. They were particularly interested in the patterned samples as great alternatives to laminates. They also provided us with some pattern direction which we were able to implement in our next round of samples,” said Ruben Bake, Mass Transit Business Manager.
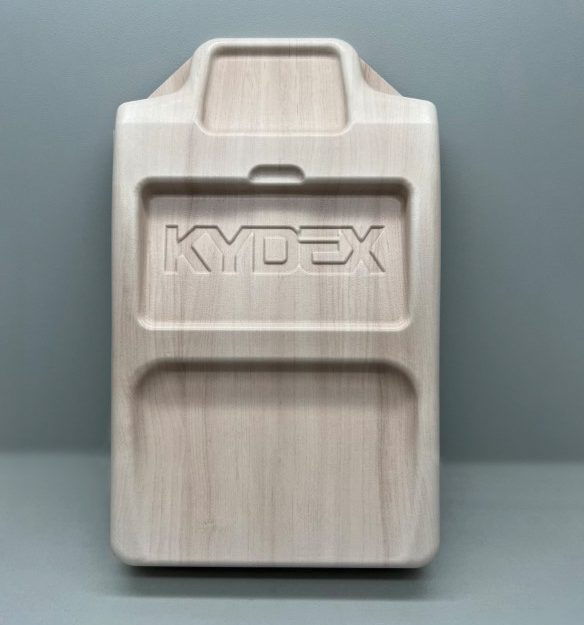
inside appLab™ and designLab®
Innovation Centers
While the appLab™ team was working on tool design, the designLab® team was developing patterns and selecting colours for the final parts. Their goal was to showcase the benefits of integral colour and Infused Imaging™ technology utilizing PVDF capped materials, compared to metal or fiberglass that is traditionally painted. “One of the greatest benefits of using Infused Imaging™ on capped KYDEX® Thermoplastics, is that customers can create custom panels with orders as low as one sheet!” said Karyn McAlphin, Creative Design Lead.
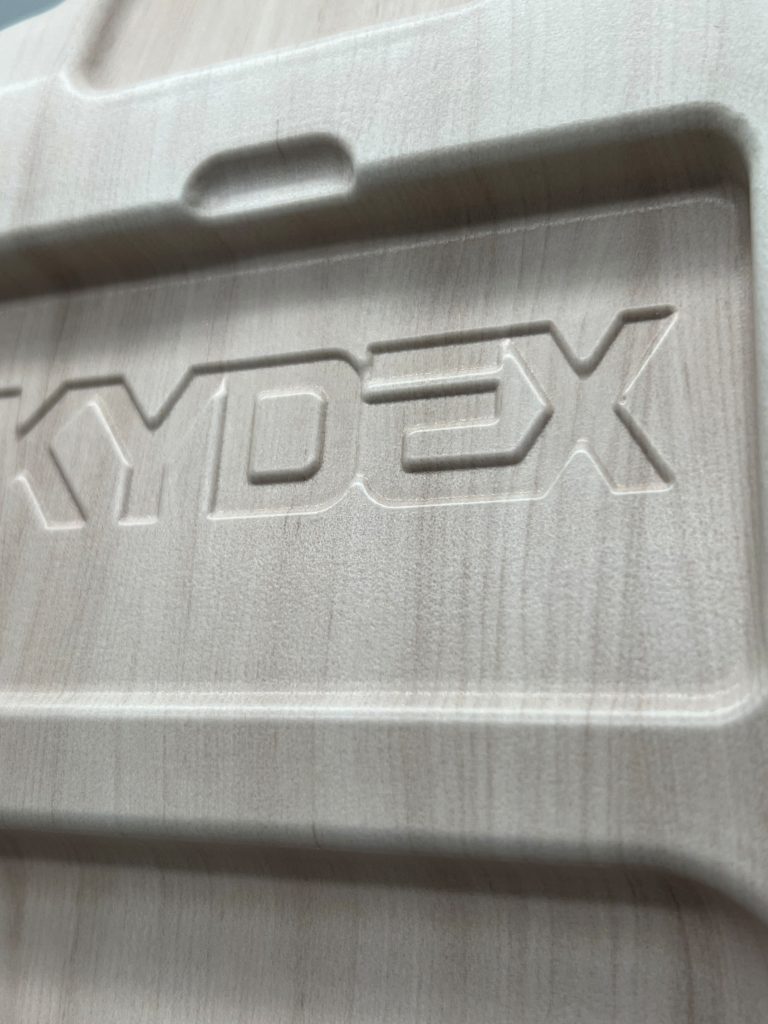
Infused Imaging™ technology embeds the pattern into the sheet rather than on it, allowing custom quantities and increased quality. Importantly, it won’t chip, fade, or delaminate like other materials, and because the design permeates the capped material, it retains the anti-graffiti and cleanability properties of the PVDF film. The team then pressure-formed a full set of positive and negative parts using the textured tool in time for the RedCabin Railway Interiors Innovation Summit.
Utilizing rapid prototyping and industry-leading design, the teams delivered on their mission to create a versatile and educational part for the Mass Transit Industry. As collaborative partners, SEKISUI KYDEX puts innovation at the forefront of their business by guiding customers through the project from beginning to end. The experts inside the Innovation Centers, designLab® and appLab™, are available to our partners to help identify the best solutions for their applications.
Read the full story here: https://kydex.com/innovation-stories/innovation-story-rapid-prototyping-seatback-for-rail-interiors-inside-applab-and-designlab/
Ian Donohue, Digital Marketing Communications Manager, SEKISUI KYDEX
SEKISUI KYDEX innovates and creates sustainable thermoplastic material solutions for the next generation of product design. SEKISUI Chemical’s corporate commitment to Speed, Service, and Superiority is realized through the KYDEX® Thermoplastics’ business model of manufacturing bespoke materials with short lead times in small quantities. This Quick Response Manufacturing (QRM) model at three manufacturing campuses expands beyond thermoplastic sheet. The KYDEX® portfolio also includes injection molding resins, proprietary Infused Imaging™ technology, integral special effects, unique textures, and custom products and design.
The SEKISUI KYDEX appLab™ and designLab® Innovation Centers are collaborative spaces for clients and customers to bring the supply chain together for rapid prototyping and design development. These spaces are the bridge between engineering and art. More than 300 dedicated professionals in Bloomsburg, PA, and Holland, MI, working with a global network of sales and distribution partners, are committed to delivering more than their customers can imagine. Visit kydex.com for more information.