Caltrans Designs Unique Bridge-Plate Device
By Berinder Dhaliwal | 12/19/2024
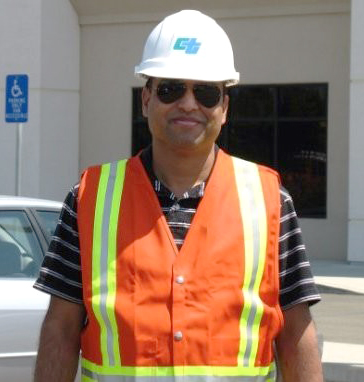
BERINDER DHALIWAL
Senior Transportation Engineer
Office of Project Development, Management, & Delivery
California DOT (Caltrans)
Intercity train operation and other modes of passenger rail service often need to contend with boarding passengers spanning a horizontal gap between the edge of an elevated train station platform and the door threshold of the railcar. For high-level platforms at 48 inches above top of rail, these specified gaps can be more than 36 inches. At this distance, a mechanical bridging device is needed to facilitate safe passenger boarding across the gap.
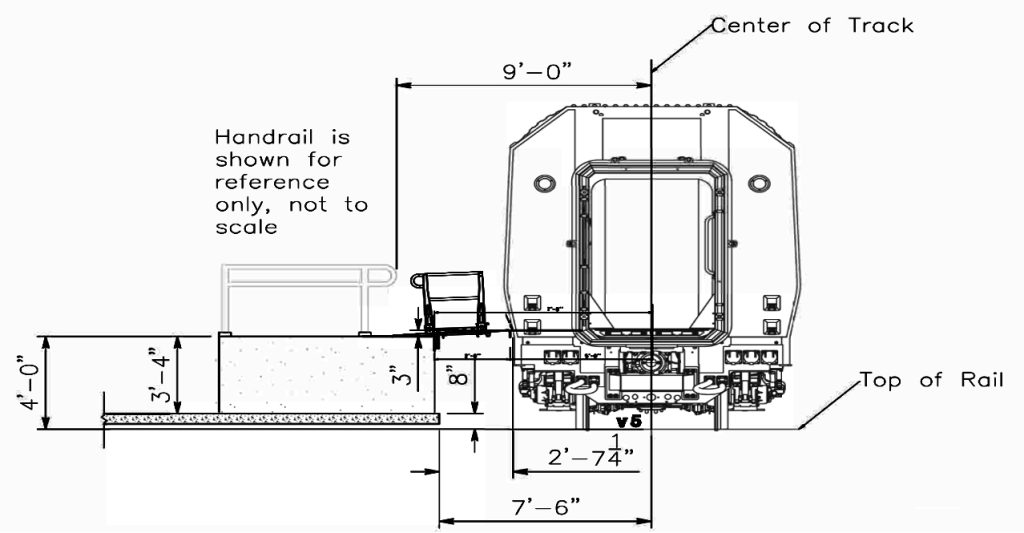
The specified lateral setback distance of the platform measured from the track is controlled by many factors, including the need for clearance to accommodate dynamic motion of railcars passing stations, regulations, and track owner requirements to accommodate wide freight loads that may include large industrial machines or commercial aircraft parts, such as fuselages. In California, this setback has been established by regulations and specifications to facilitate inter- and intra-state commerce, including those from the California Public Utilities Commission (CPUC), the Strategic Rail Corridor Network (STRACNET), Association of American Railroads (AAR), and by specific freight railroad owners on whose right of way Caltrans operates its fleet. For California, the CPUC is the controlling regulation, requiring a gap that is specified in CPUC General Order (GO-26D), which is 18 inches wider than requirements of STRACNET.
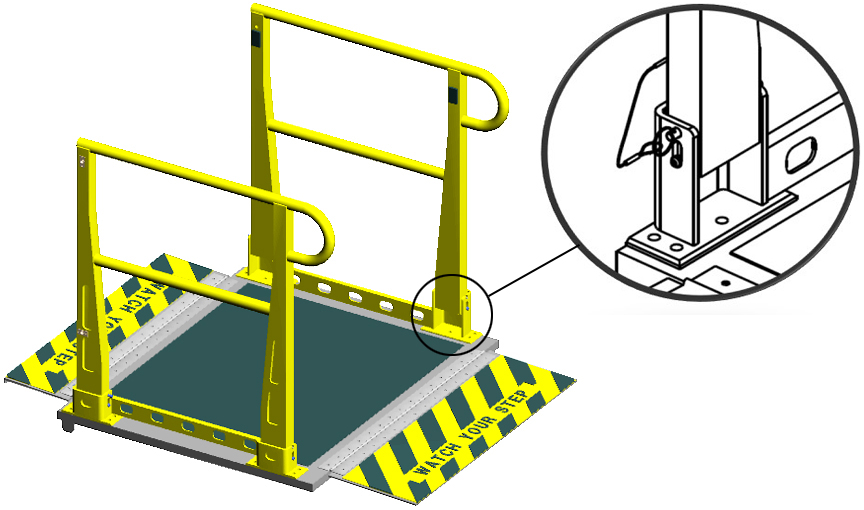
To meet this requirement, California DOT (Caltrans) has designed a unique bridge-plate device, that spans a horizontal gap of 36 inches, for revenue operation of its new, state-of-the-art Siemens Venture coach cars now in service along the Amtrak San Joaquins corridor between Oakland, Bakersfield, and Sacramento, which serves 800,000 passengers a year. This bridge-plate device will serve as backup to a permanent car-borne automated bridging system now in final stages of design.
The required length of the Caltrans designed bridge-plate is long enough to need safety handrails on both sides of the plate per ADA requirements. Other constraints influencing the design include weight and size limits to ensure easy deployment by conductors, and safe folding handrails to permit storage and handling of the bridge plate. For this design, Caltrans introduced an innovative bridge plate made from lightweight composite material for the plate structure, with a unique locking foldable mechanism for the handrails attached to the plate. The honeycomb composite plate construction is lighter than aluminum or even titanium but without the loss of strength—not unlike the material structures used in aircraft and some automotive applications.
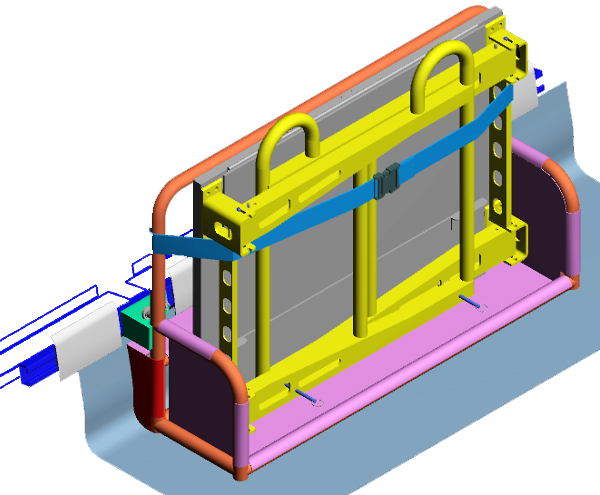
The plate is strong enough to support 800lbs of weight, accommodating passengers with powered wheelchairs. The foldable mechanism for the two handrails is essentially attached to the plate using a pinned hinge with a box-like captive support to allow handrail rotation that locks in place when extended. Locking is important to prevent unintentional collapse or rotation of the handrails, which could lead to risk of passengers falling on or off the bridge plate and onto the track.
The bridge plate, when deployed, provides ample side clearance for wheelchairs to facilitate unassisted level-boarding of passengers in accordance with ADA guidelines. When not in use, the device will be stored onboard in a dedicated fixture that is secured to the structure on an inside wall of the railcar.
Caltrans has designed a solution to provide level boarding for its new rail assets in compliance with all applicable FRA Code of Federal Regulations (CFR), CPUC, ADA, and OHSA regulations. Caltrans intends to have these bridging devices fabricated and deployed for service in 2025.